SmartFactory-KL production line
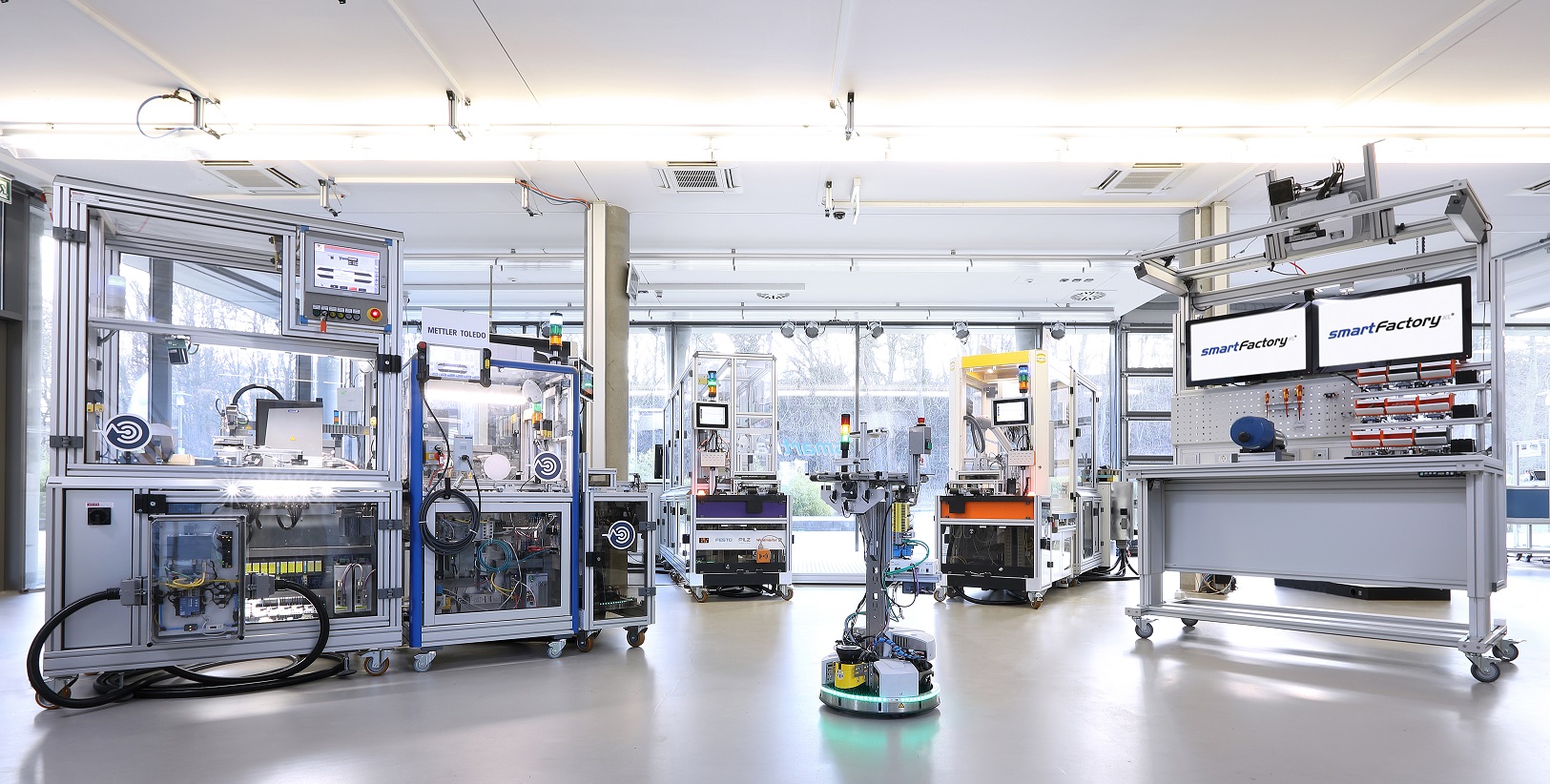
The Industry 4.0 plant of the SmartFactory-KL partner group enables flexible production due to its modular design. Source: SmartFactory-KL/A.Sell
The story
SmartFactory-KL is a manufacturer-independent demonstrator and research platform, where innovative Information and Communication Technologies (ICT) are evaluated and further developed in a realistic, industrial production environment. By being a pioneer of Industry 4.0, SmartFactory-KL secures a decisive competitive advantage for the factories of the future.
The Challenge
Due to the ever-changing customer demands, today's manufacturing SMEs are increasingly exposed to growing complexity. Companies must ensure that individual products continue to be manufactured cost-effectively, yet still, meet the same quality requirements as series-produced products. Due to this, the demands placed on factory workers are constantly increasing. The workers must keep track of which products have to be manufactured where and in which order, recognize quality defects as quickly as possible, and at the same time know what to do with the product in the event of rejects. Undoubtedly, new digital technologies are needed to reduce this complexity as efficiently as possible, as well as to support people in production appropriately.
The solution
To deal with this challenge, new cognitive technologies were developed within the framework of the AUTOWARE project and prototypically tested at SmartFactory-KL. First and foremost, access to information was improved by the introduction of an Active Digital Product Memory (ADOMe). This product memory stores all the information required to manufacture an individual product when an order is received.
.png)
The product memory communicates via binary communication protocols with a "Trac'n Trace" software, which records current information from the product memory, compares it with the information stored in the server (or ERP - Enterprise Resource Planning - system) and updates it according to the level of information.
The Active Digital Product Memory guides the product independently through the production line. This means that no wrong production step can be carried out on a product. At the same time, each product can be addressed directly through continuous communication so that the position of each product is known at all times. Any change in the production sequence, e.g. because of the cancellation of a customer order, can also be adjusted rapidly.
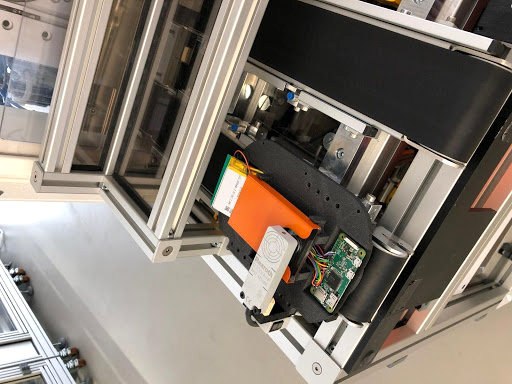
In the neutral test factory SmartFactory-KL, the fog node is attached in the edge layer. The fog node has several virtual machines that are used to realize the different applications scenarios in the SmartFactory-KL. In the first case, Tomcat is installed on the fog node server running the visualization software DyVisual. The DyVisual software represents a real-time capable visualization of the production plant (a "digital twin" of the plant) and can be accessed via compatible web browsers at any time and from any location.
This makes it possible to obtain information remotely about the current status of the system. The implementation of the server close to the machine on the edge device makes it possible to update it at any time by means of current information about the OPC UA (Open Platform Communication Unified Architecture) messages, so that the web model of the plant can be animated in almost real time. This Tomcat server runs on the operating system, Windows 10 with 64bit.
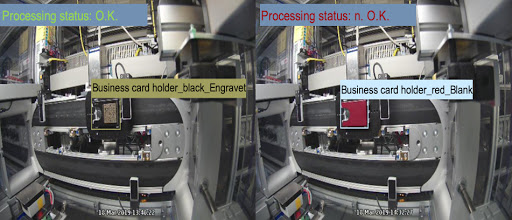
In addition to the visualization of the system, the operator is also supported by an augmented reality solution. A data goggle (in this case a Microsoft Hololens) is used to provide the operator with an insight into the internal processes of the modules without having to actively shut them down and open them. This shows the operator which components and which products the operator sees in front of him/her. In this way, the operator takes the right steps in the event of rework and does not waste time searching for instructions. The components are recognized in the Edge and visualized in the data glasses.
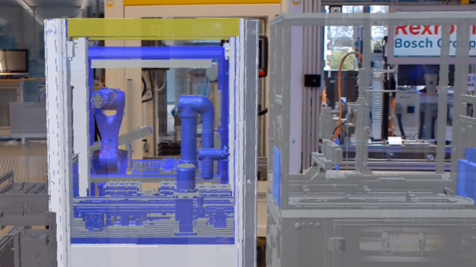
To supplement the above mentioned technologies, SmartFactory-KL has introduced an algorithm that dynamically reschedules the production sequence when ordering or cancelling products. In this way, the products can be addressed directly, so that the products can reorganize themselves in the production independently. In addition, artificial intelligence techniques were used to take over flexible quality monitoring in the plant. This was introduced in the form of visual quality control, which can dynamically record the condition of a product and forward this information.
The results
By introducing active product memories, previous problems with the identification and rearrangement of products were solved completely autonomously. The use of the Active Digital Product Memory with integrated asset administration shell has proven to be an enabler of autonomous, robust production. By directly addressing the products, further use cases, such as the optimization of the production sequence or the reaction to quality defects, can be effectively integrated into a system.
The developed technologies can scale strongly in all productions with discrete manufacturing (piece goods manufacturing), as well as benefit automated productions (through active product memories and intelligent visual quality control) and manual productions (through Smart Worker Data Glasses).