Industrial Cooperative Assembly of Pneumatic Cylinders

Support of the manual assembly process of pneumatic cylinders by the use of human-robot collaboration.
The story
SMC Germany is the leading manufacturer of pneumatic components, electrical automation technology and partner for individual customer solutions. With focus on resource and energy efficiency, security and flexible production SMC provides its customers decisive competitive advantages. The local factory has the strategic task of offering customized product solutions in a short delivery time for small and middle lot sizes. The main assembly work of pneumatics cylinders based on manual working steps. Based on the variances of many different compact cylinder and series in different specialization, diameters and strokes. People need to be trained so they understand the different requirements for different products.
The Challenge
The main business objective is the support and improvement of the manual assembly process of cylinders by using collaborative robotics. Humans should be relieved from assembly tasks that can be better handled by cognitive robots, to increase effectiveness and productivity. This is achieved by letting humans do what they can do best and let robots do complementary tasks, reducing human intervention by implementing a Human-Robot-Cooperation approach. The aim is to increase the flexibility by rapidly switching from one product variant to another, and maintaining constant scalability with respect to the assembly of individualized products. Additionally, an increased efficiency of the employee is achieved by transferring non-value-added activities and monotonous repetitive tasks to the robot. This will help to ensure the consistently high-quality level of SMC products.
Regarding the product quality SMC expects 100% reliable quality measuring and documentation of material length and dimensions of the final product. This documentation of the quality measuring process will serve for verifiability of potential quality complaints by customers. The AUTOWARE approach will help to realize the process of quality inspection and documentation as a human-robot cooperation.
The solution
By implementing the AUTOWARE technology developed by Fraunhofer, which is an internationally leading organization for applied research in Visual Computing, some of the manual and repetitive assembling steps could be automated if the use case results were to be introduced in the factory to reduce the assembly time and manufacturing costs. The special focus was put on the autonomous quality assessment and protocolling of assembly states to relieve the human from cognitive demanding examining tasks.
As a functional requirement, the system receives the instructions from the scanned manufacturing order and extracts all production information (PMI) and workflow from the CAD models. The protocolling is then used to track and comprehend the manufacturing process of every part and to assure a high-quality standard. For the SMC use case, Fraunhofer developed an automated 3D laser scanning station. Upon request, the station scans the part located on the scanning platform. The system automatically detects in which state the part is and extracts desired quality checks from annotations in the CAD model. After that, the application autonomously performs quality checks on the part, e.g. measuring heights, detecting contamination, and taking further scans or photos for archiving, if required.
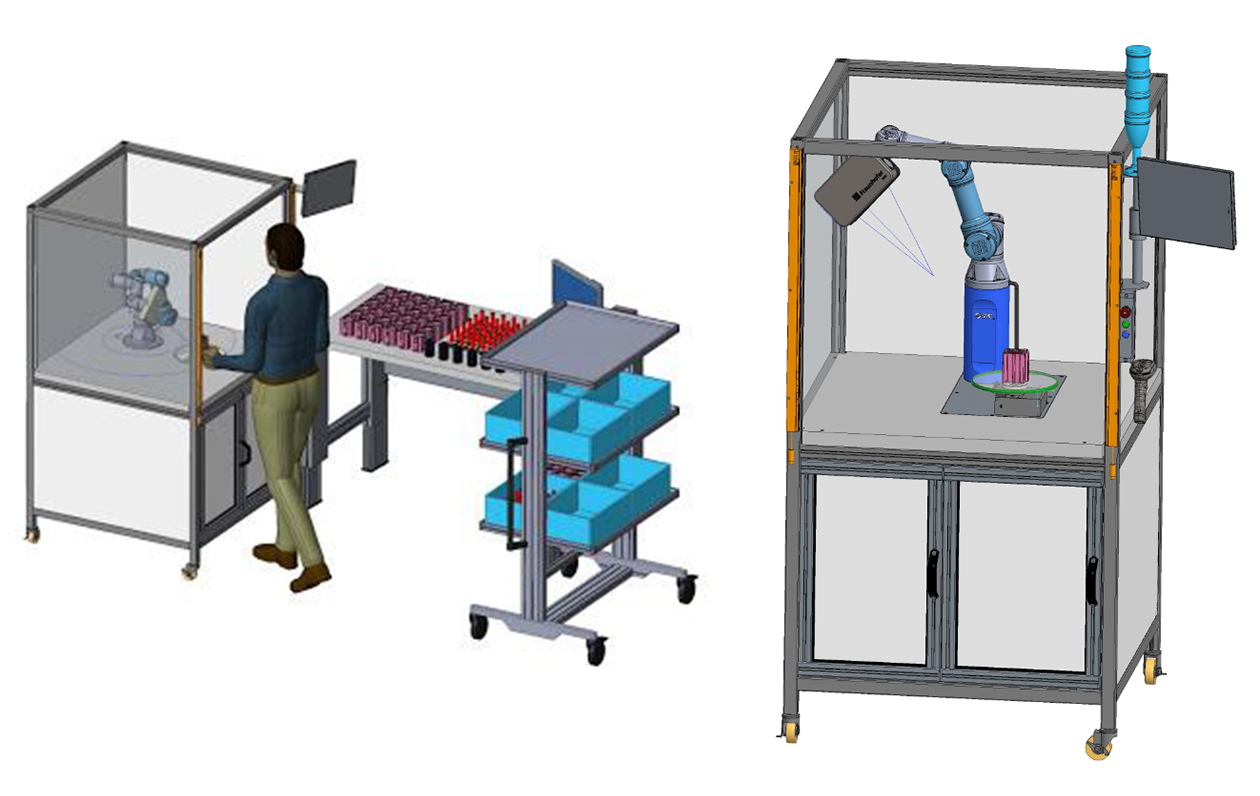
The results
The use case results provides the possibility of manufacturing SMEs to develop digital cognitive automation systems. This allows the enrichment of production facilities with cognitive abilities. The developed technology can be integrated in flexible manufacturing systems, which belong to sectors where individual customer solutions in small and middle lot sizes in short lead times and high flexibility are required. As a result, SMEs can benefit from the savings in manual work and higher quality of the products.