Collaborative workcell for assembly & logistics
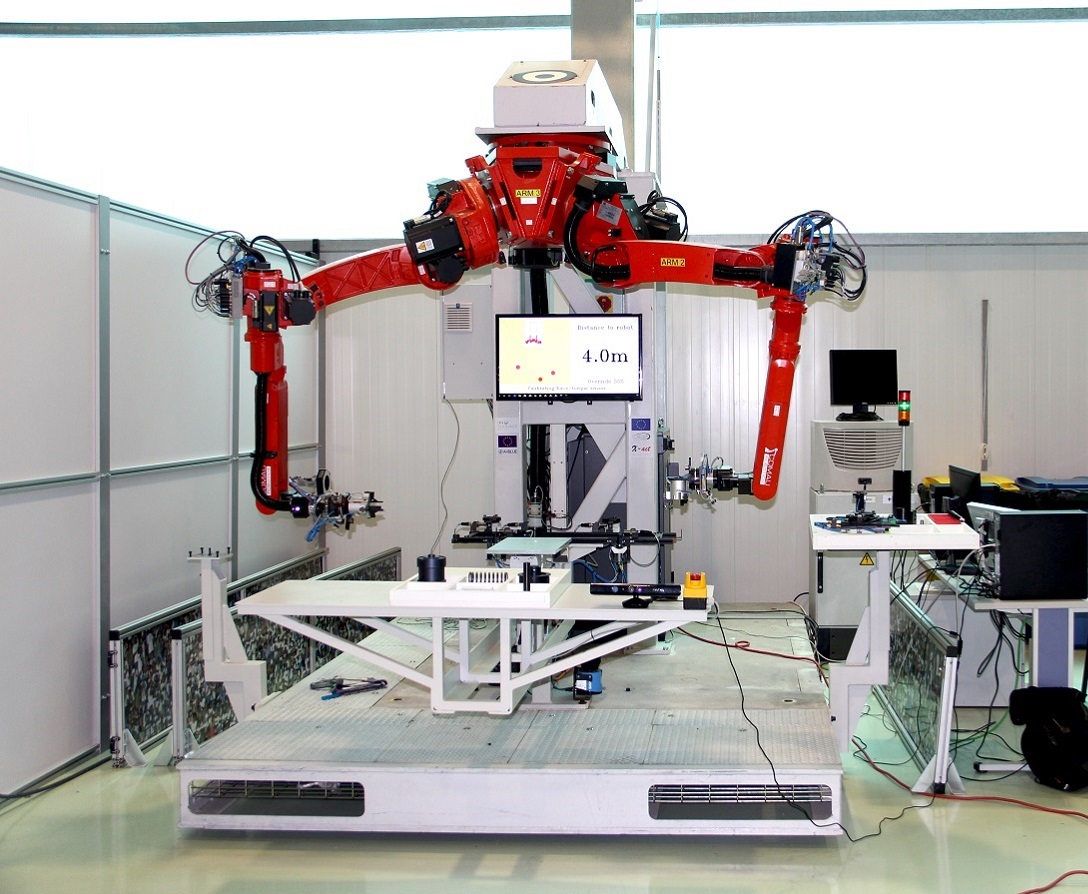
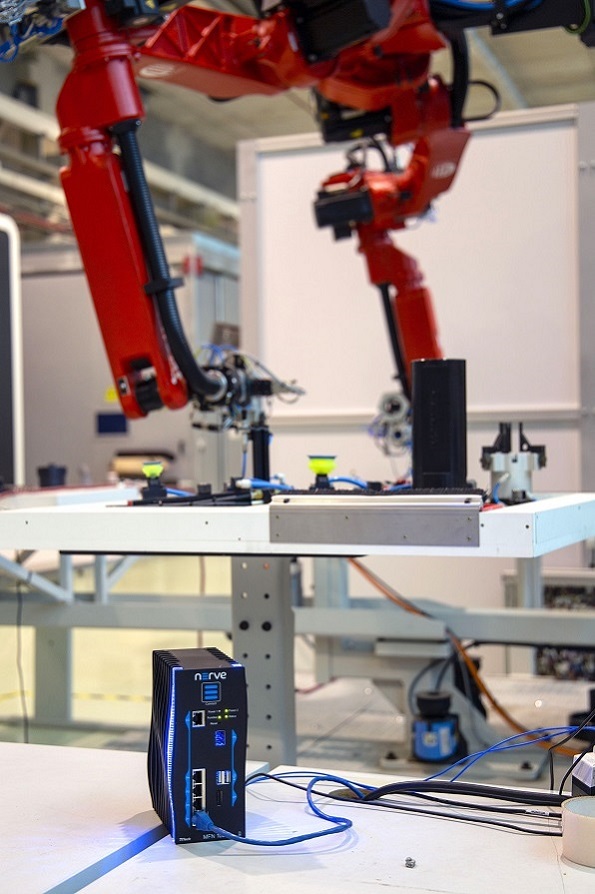
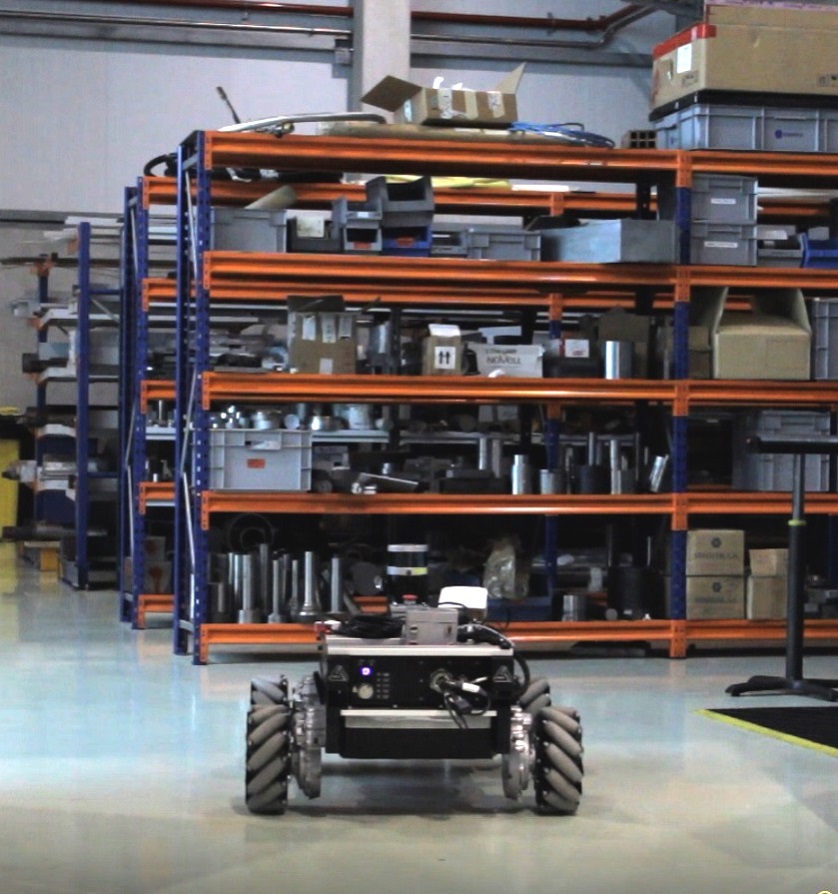
Neutral experimentation infrastructure for intelligent automation applications for robotic industrial scenario.
The story
IK4-TEKNIKER is a technological research centre that aims to develop technology to improve industrial competitiveness. The main aim of IK4-TEKNIKER’s lab scenario, which serves as a technology demonstrator, is to enhance collaborative robotics-related technologies, as well as to provide automation solutions with high reconfigurability and flexibility in robotic working cells.
The Challenge
The main challenge of IK4-TEKNIKER’s robotic workcell before the AUTOWARE project was its low adaptability to external conditions. The cell could execute different assembly operations with autonomy and a certain degree of adaptation, which were coming from vision and force sensors, but the adaptation to new references or process changes (e.g. lack of parts) was low.
In a typical scenario at IK4-TEKNIKER, a mobile robot is responsible for fetching objects to a robotic bi-manipulator. A human operator is in charge to manually load the objects on the mobile robot from the shelves. Centralized wireless or wired communication infrastructure allows both the robot and the operator to be aware of which object is currently needed at the bi-manipulator.
However, due to the harsh conditions in several industrial environments, it is not unusual for the main centralized operational network to go offline, for a variety of reasons. If that happens, the mobile robot and human operator cannot be aware of which object is currently needed at the bi-manipulator. This can result in a failure of the production process.
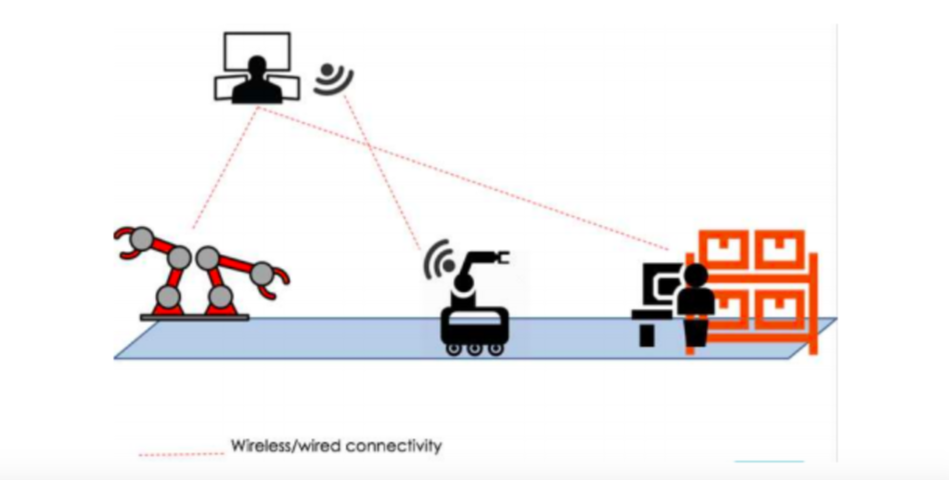
The solution
To address the challenge, AUTOWARE partners TTTech, a Vienna-based technology leader in networked safety controls, in close collaboration with Universidad Miguel Hernández de Elche (UMH), the Institute of Informatics and Telematics of National Research Council (IIT-CNR) and IK4-TEKNIKER, have developed the Smart Data Distribution enabler, which is a core component in the AUTOWARE communications and data management framework.
It implements the logic of a control plane for cognitive data distribution across all communication layers of AUTOWARE architecture. It is based on the available communication technologies and is supporting the needs of the higher-level services and applications. The AUTOWARE Smart Data Distribution enabler is decentralized, dynamic and hierarchical, to support cooperation with cloud-based service provisioning and communication technologies.
More specifically, it provides decentralized data distribution among the various nodes of the AUTOWARE ecosystem. This decentralization is targeting the efficient management of massive data generation and consumption and the exploitation of resources available locally at individual nodes. Then, it copes with dynamically changing network parameters by employing adaptive data placement and replication techniques. Finally, it provides a hierarchical data management, by applying a mix of centralized and decentralized control processes and a hierarchy of data managers.
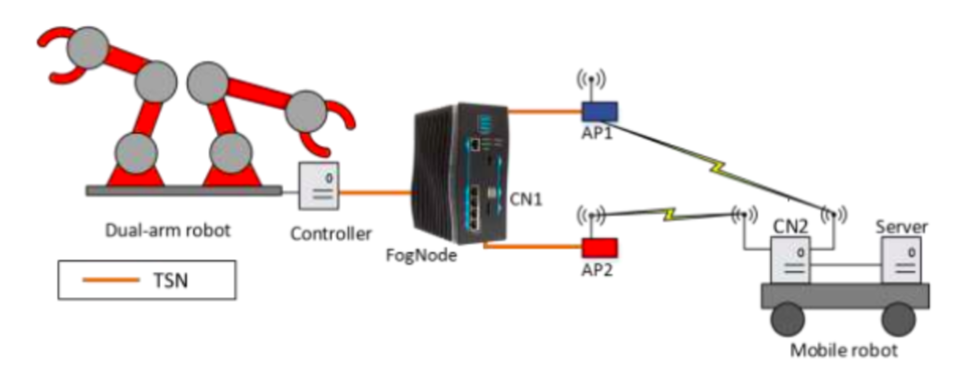
The open CPPS platform (i.e. fog node) was integrated as a central station, where the configuration of the open platform was performed with the usability enablers for programming and controlling the fog node. The node acted as a central point, where the different applications (e.g. data management) were hosted. The robot controller and available access points were connected to the fog node and enabled communication between the various components in the production cell. The Smart Data Distribution enabler had achieved a high fault tolerance and reliability with low-cost.
The developed technology can be applied in the following scenarios within the shopfloor:
- A dual-arm robot with operator/worker (without mobile platform).
- A dual-arm robot with operator/worker & mobile platform where the operator handles the transport process when the mobile platform is not available.
- A dual-arm robot with a mobile platform (fully automated).
- A dual-arm robot with a mobile platform & other technologies supported by different communication & fog deployments (infrastructure-based, lightweight communication, fog node).
In all four above described scenarios, the Fog Computing Solution creates value by providing stable communication, which is the most important service to build robust coordination among CPPSs. Moreover, stable and redundant communication routes are provided by IIT-CNR and UMH.
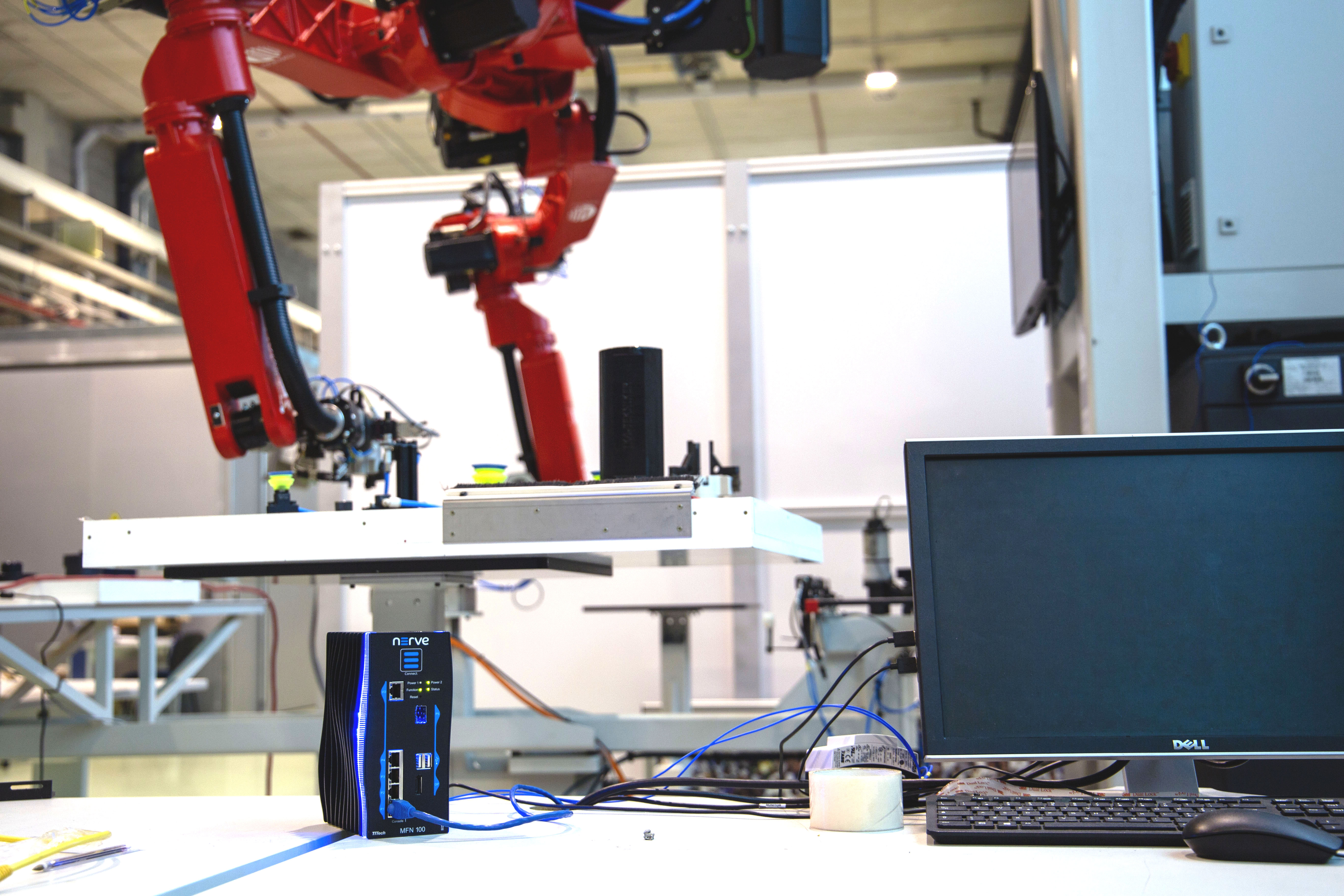
The results
The AUTOWARE project has provided mechanisms for building a flexible, collaborative work cell that can solve the coordination of different production resources. Thanks to better communication between the various elements of the robotic cell (dual-arm and mobile robot), the number of stops, which were caused by the lack of materials, has decreased.
The developed technology can mainly be used by IK4-TEKNIKER’s production resources to connect and robustly communicate with each other. This technology can also be applied in the manufacturing sector, where the focus is on complex products with short production cycles, and where different automation solutions with high reconfigurability and flexibility need to be provided.
The proposed scenario is aligned with the needs of incorporating robots able to safely and adaptatively co-operate with humans in manufacturing operations. The mobile robot platforms can be used in an environment with limited space that requires precise mobility and handling.
Based on that, AUTOWARE has provided solutions that can lower the barriers of manufacturing SMEs to have their systems connected and communicating with each other in a reliable infrastructure. This leads to a higher contextual adaptation and flexibility in their manufacturing processes. Such features are required for the new emerging markets in which product variations and mass customization are increasing.